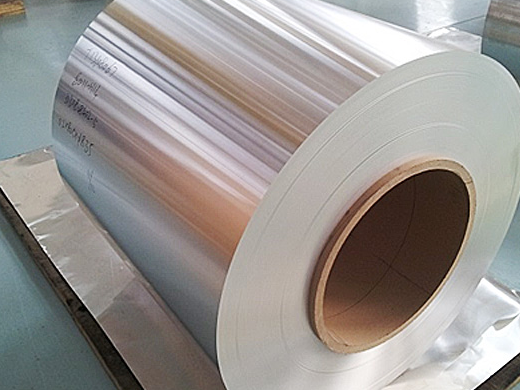
Cold formed aluminum foil is at the heart of alu alu OPA/Al/PVC sandwich foils used for pharmaceutical blister pack applications because of their inherently superior advantages. Aluminum, even in micron thickness, is the best vapor and light barrier besides providing aesthetic shine for pharmaceutical blister packs.
Pharmaceutical Cold forming foil is made of aluminum foil, nylon (oPA) and PVC films, by using dry bond lamination technology. As blisters are formed at room temperature, without heating, so it is called as cold forming blister laminated foil.
Cold forming foil is one type of triplex packaging material, between each two layers, there is adhesive for lamination. The adhesive we are using is imported from USA, to ensure good performance during cold forming process, such as no delamination and cracking.
Cold-formable material is commonly pressed aluminum that is laminated with plastic. The aluminum is resistant to many outside forces and has high mechanical resistance; aluminum has a tendency to leech into other materials and to crack, but the plastic inclusion corrects these issues. Thermoformable materials are plastics that can be easily molded into any shape, but they are not as resistant to outside forces — especially light — because the plastic is transparent. If the product is a simple shape that needs high resistance, then cold-formable materials are likely best;
Cold Forming Blister Foil(Alu-Alu) is one kind of blister primary packaging material for solid pharmaceuticals, like tablet & capsule.
Cold Forming Blister Foil Features
100 % barrier against water vapor, gases, light etc.
Excellent formability
High degree of thermal stability
High malleability for deep drawing blister cavities
High aesthetic appeal
Sealable with aluminum lidding foil
Colorful surface as RAL color-list
The PVC film in alu -alu laminate is commonly used as the contact layer and seal to the lidding foil on pharmaceutical blisterpack (as neutral layer for the goods to be filled).
PVC is very stiff and does not tend to shrink or spring during cold forming. Once the cold forming process is complete, the PVC helps the cavity hold its shape. In short, it ensures the geometric stability after cold forming.
The nylon (oPA) film is mostly responsible for the multi - axial forming. Laminating the aluminum with the oPA film doubles the formability of the blister.
Related Comments